Lite Foot, like many of my projects, began as one thing, but took on a life of its own and ended up being something I didn’t completely anticipate. Simply put, I started out building an ultra-light P3 as another way to achieve extended flight.
Frankly, I wasn’t optimistic about this goal from the start because the Phantom 3 really is a pretty light copter to begin with. This goal came from concluding that DJI had gone to great lengths to design a battery manager that not only could take good care of an HV lipo battery, it could also read more than just its voltage. DJI went to great lengths to design the thing to make sure it could detect the presence of additional battery capacity, and defeat it. Presumably, to maintain control of its product and to make sure aftermarket suppliers could not make it competitive with its future products? It took me a while to come to this conclusion, and I made up plenty of new profanity in the process. I also learned to dislike my new, favorite corp DJI, like I have never disliked a manufacture before. Everything from the way they treat their customers to the underhanded way they implement firmware updates, which can’t be trusted anymore. For something like a drone with safety issues all over the place, this really sucks.
P4? You have to be kidding… (my own personal thing guys, no offense P4 owners – please enjoy) I do like the P3 pro very much and have a significant investment in it. I am either going to continue with it and expand it if it continues to open up, or move to another platform. As hard as I am on DJI, my hat is off to them for the P3 pro. It is the perfect everything. Size, etc… What I have done with my Lite Foot project is an example of how it may be expanded with exotic materials and tele-photo. Call this a P3 compatible. Like a VW bug. The P3 is a pretty big, horizontal success, and my guess is that parts should be available indefinitely.
Back to Lite Foot. Originally it was simply P3- Ultra-Light. I am easily distracted, especially when it is something that may give my project a cool, Indian sounding name. If I stayed strictly true to my theme, I would not have put the cool feet on Lite Foot. They cost a good 50 grams, or so. As I was testing the ultra-light, it became clear this was going to be a work horse. Everything about it wanted to stay in the air. It is so easy to service. Btw, I have learned to lubricate my motors. I didn’t think these sealed bearings needed it, but it makes a huge difference. I actually designed the motor mounts to make this easy. I also provide air vents and use the second version motors. They run slightly warm to the touch (instead of really hot).
The work horse did need good markings to use it easily. This copter is fitted with a Ragecams adapter and takes various different size tele-photo lenses. So, it is often at a distance when run visually. Where to put the LED’s so that they don’t interfere with the camera work? Put them on the feet, of course.
This design uses a modified stock P3 smart battery that is split into two, 2s sections. This facilitates the shorter, vertical profile. It is probably a little lighter since it loses the housing pieces. This shorter vertical height requirement makes it possible to expose less surfaces to the wind, and was the reason for it. Despite its light weight, Lite Foot does not get thrown around very much in the wind.
Oh, so what did I get after all of this? Yeah, I was right, the P3 is hard to beat on the weight, but I did, by about 120 g’s and I don’t need to add a thing. With the standard, single battery, I get a reliable 22-minute flight time as reported from the battery screen (see attachment) This is quiet flight, btw. The noise issue was one of my original motivations that I forgot about, but quickly realized how important it was to me during my testing. This is a quiet bird. My neighbors used to complain, especially when I started doubling up the batteries (they get louder). The 120 g’s make a significant difference. The copter sort of loafs in the air.
Also, as I indicated, I don’t need to add anything. Check out how high the camera is and how wide the stance is. It is a very stable platform for my camera work, far superior to the standard P3 – why(?), dunno. Drives like a 911 without the over-steer.
Now that I have fixture and templates: The next frame is going to be a strict Ultra-Light. The P3 really doesn’t need the LED’s although it does use them for communicating many things. Perhaps I will use very small LED’s, instead of the stock ones, or a fluorescent paint job.
I put a (hard-won) piece of documentation concerning extended flight in a PDF here. I think you guys deserve it. DJI shouldn’t be jerking us around with our own technology. Cheers.
This frame is also meant for serious extended flight, as well and I will do that shortly. Since it will do 22 minutes normal, I have high hopes for the extended form. To go extended I would be giving up quiet flight and performance. Twenty-two minutes is enough for almost everything, but there will be applications where you simply need time in the sky. Extending is a matter of strapping a second set of split 4,480 mah batteries onto the frame rail – the side the name is on.
Totally-Optional Reading:
Just to expand a little bit on what drives my DJI/China venting, and please don’t for a minute, mistake this for anything past corporation or country, I absolutely don’t view ethnicity at all in my vents.
How about this battery manager DJI is so proud of? Sure, it does take care of the battery, and the charging hardware is built into it. The jury is still out on the automatic discharge-to-storage mode. I just haven’t seen it work reliably. Fly your drone and observe the voltage on the transmitter, and eventually have it over-rule pilot based on battery health and land drone. Very impressive.
Impressive until you try to add battery capacity to the vessel and observe the results. The results don’t jump out at you, you have to digest them. But they are there if you are knowledgeable about healthy lipo cell voltages. If you had connected your added capacity in the logical place, where it could be managed by the battery manager switch, what you would be observing on the transmitter would be early alarms that you are running out of battery. At the same time, it would be reporting a nice, green high voltage for each cell.
What I finally realized is that the battery manager is also watching amperage, or motor load. It is not only watching, but if it decides it is high enough to be the weight of more battery it kicks its land-no-matter-what timer in to defeat our attempts to extend the range, cleanly.
As I have documented, this can be defeated by injecting the added current directly ahead of the battery manager, where it doesn’t have a chance to monitor it through its circuitry. There is still the general power to weight physics ratio to contend with, but that is under the users control.
As a side note on this successful extended flight method, since it is un-switched, it is awkward as hell. No one seems to document how to use it properly and one will always be forgetting to plug-in, or un-plug at the right time. Other than that, it seems to work just fine
....
Another side note in reference to the above, if a NO (normally-off) relay were put into the assist circuit, energized by the general system power, in theory I believe this would become a no-brainer, and easy to use. One could even set up and plug-in the assist batteries in advance without the bird going live. I’m not sure about the drain of the relay, and if it is worth it. Maybe someone could do the math. The relay could be replaced with a switch (w/led). Obviously I haven’t tried any of this, but will be soon.
OK, as I indicated, it took me a while and a ton of cuss words to get here. As far as I am concerned, if DJI wants to play these games, they are bringing it on themselves. These products of the thousand-year-old civilization (re: philosophy, values..) would probably say it is their right to protect their product and that would be living in a dream world. The reality would be more like DJI giving elaborate reasons of how these things the battery manager are doing are necessary to verify the health of the battery. You know, the DJI spin - total hogwash. OK.
Consider this, however, and this is the reason you wouldn’t find this sort of thing in a domestic product of this nature. These drones are pretty elaborate devices. Things do go wrong sometimes, unexpectedly. To make something as vital as the battery manager unnecessarily complicated, and I mean 10 times as complicated as it needs to be, is ridiculous. I consider it irresponsible. This is a safety issue. DJI has put their future competitiveness ahead of safety.
How many times have you heard of an un-explained drone disappearance? The battery manager has the authority to shut the drone down. It is almost statistically impossible that failure of their proprietary flight time system hasn’t been the cause of many of them. It is the most complicated part of the battery manager.
Do you think DJI fesses up about drone incidents caused by battery manager logic failure. The logic should be only: Is the voltage high enough? That’s all. There is not much that will go wrong with that.
YouTube Link:
phantom4 zoom lens telephoto modification Ragecams inspection Search & rescue wa | HD Wearable Video Custom Mods By RageCams
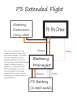
Frankly, I wasn’t optimistic about this goal from the start because the Phantom 3 really is a pretty light copter to begin with. This goal came from concluding that DJI had gone to great lengths to design a battery manager that not only could take good care of an HV lipo battery, it could also read more than just its voltage. DJI went to great lengths to design the thing to make sure it could detect the presence of additional battery capacity, and defeat it. Presumably, to maintain control of its product and to make sure aftermarket suppliers could not make it competitive with its future products? It took me a while to come to this conclusion, and I made up plenty of new profanity in the process. I also learned to dislike my new, favorite corp DJI, like I have never disliked a manufacture before. Everything from the way they treat their customers to the underhanded way they implement firmware updates, which can’t be trusted anymore. For something like a drone with safety issues all over the place, this really sucks.
P4? You have to be kidding… (my own personal thing guys, no offense P4 owners – please enjoy) I do like the P3 pro very much and have a significant investment in it. I am either going to continue with it and expand it if it continues to open up, or move to another platform. As hard as I am on DJI, my hat is off to them for the P3 pro. It is the perfect everything. Size, etc… What I have done with my Lite Foot project is an example of how it may be expanded with exotic materials and tele-photo. Call this a P3 compatible. Like a VW bug. The P3 is a pretty big, horizontal success, and my guess is that parts should be available indefinitely.
Back to Lite Foot. Originally it was simply P3- Ultra-Light. I am easily distracted, especially when it is something that may give my project a cool, Indian sounding name. If I stayed strictly true to my theme, I would not have put the cool feet on Lite Foot. They cost a good 50 grams, or so. As I was testing the ultra-light, it became clear this was going to be a work horse. Everything about it wanted to stay in the air. It is so easy to service. Btw, I have learned to lubricate my motors. I didn’t think these sealed bearings needed it, but it makes a huge difference. I actually designed the motor mounts to make this easy. I also provide air vents and use the second version motors. They run slightly warm to the touch (instead of really hot).
The work horse did need good markings to use it easily. This copter is fitted with a Ragecams adapter and takes various different size tele-photo lenses. So, it is often at a distance when run visually. Where to put the LED’s so that they don’t interfere with the camera work? Put them on the feet, of course.
This design uses a modified stock P3 smart battery that is split into two, 2s sections. This facilitates the shorter, vertical profile. It is probably a little lighter since it loses the housing pieces. This shorter vertical height requirement makes it possible to expose less surfaces to the wind, and was the reason for it. Despite its light weight, Lite Foot does not get thrown around very much in the wind.
Oh, so what did I get after all of this? Yeah, I was right, the P3 is hard to beat on the weight, but I did, by about 120 g’s and I don’t need to add a thing. With the standard, single battery, I get a reliable 22-minute flight time as reported from the battery screen (see attachment) This is quiet flight, btw. The noise issue was one of my original motivations that I forgot about, but quickly realized how important it was to me during my testing. This is a quiet bird. My neighbors used to complain, especially when I started doubling up the batteries (they get louder). The 120 g’s make a significant difference. The copter sort of loafs in the air.
Also, as I indicated, I don’t need to add anything. Check out how high the camera is and how wide the stance is. It is a very stable platform for my camera work, far superior to the standard P3 – why(?), dunno. Drives like a 911 without the over-steer.
Now that I have fixture and templates: The next frame is going to be a strict Ultra-Light. The P3 really doesn’t need the LED’s although it does use them for communicating many things. Perhaps I will use very small LED’s, instead of the stock ones, or a fluorescent paint job.
I put a (hard-won) piece of documentation concerning extended flight in a PDF here. I think you guys deserve it. DJI shouldn’t be jerking us around with our own technology. Cheers.
This frame is also meant for serious extended flight, as well and I will do that shortly. Since it will do 22 minutes normal, I have high hopes for the extended form. To go extended I would be giving up quiet flight and performance. Twenty-two minutes is enough for almost everything, but there will be applications where you simply need time in the sky. Extending is a matter of strapping a second set of split 4,480 mah batteries onto the frame rail – the side the name is on.
Totally-Optional Reading:
Just to expand a little bit on what drives my DJI/China venting, and please don’t for a minute, mistake this for anything past corporation or country, I absolutely don’t view ethnicity at all in my vents.
How about this battery manager DJI is so proud of? Sure, it does take care of the battery, and the charging hardware is built into it. The jury is still out on the automatic discharge-to-storage mode. I just haven’t seen it work reliably. Fly your drone and observe the voltage on the transmitter, and eventually have it over-rule pilot based on battery health and land drone. Very impressive.
Impressive until you try to add battery capacity to the vessel and observe the results. The results don’t jump out at you, you have to digest them. But they are there if you are knowledgeable about healthy lipo cell voltages. If you had connected your added capacity in the logical place, where it could be managed by the battery manager switch, what you would be observing on the transmitter would be early alarms that you are running out of battery. At the same time, it would be reporting a nice, green high voltage for each cell.
What I finally realized is that the battery manager is also watching amperage, or motor load. It is not only watching, but if it decides it is high enough to be the weight of more battery it kicks its land-no-matter-what timer in to defeat our attempts to extend the range, cleanly.
As I have documented, this can be defeated by injecting the added current directly ahead of the battery manager, where it doesn’t have a chance to monitor it through its circuitry. There is still the general power to weight physics ratio to contend with, but that is under the users control.
As a side note on this successful extended flight method, since it is un-switched, it is awkward as hell. No one seems to document how to use it properly and one will always be forgetting to plug-in, or un-plug at the right time. Other than that, it seems to work just fine

Another side note in reference to the above, if a NO (normally-off) relay were put into the assist circuit, energized by the general system power, in theory I believe this would become a no-brainer, and easy to use. One could even set up and plug-in the assist batteries in advance without the bird going live. I’m not sure about the drain of the relay, and if it is worth it. Maybe someone could do the math. The relay could be replaced with a switch (w/led). Obviously I haven’t tried any of this, but will be soon.
OK, as I indicated, it took me a while and a ton of cuss words to get here. As far as I am concerned, if DJI wants to play these games, they are bringing it on themselves. These products of the thousand-year-old civilization (re: philosophy, values..) would probably say it is their right to protect their product and that would be living in a dream world. The reality would be more like DJI giving elaborate reasons of how these things the battery manager are doing are necessary to verify the health of the battery. You know, the DJI spin - total hogwash. OK.
Consider this, however, and this is the reason you wouldn’t find this sort of thing in a domestic product of this nature. These drones are pretty elaborate devices. Things do go wrong sometimes, unexpectedly. To make something as vital as the battery manager unnecessarily complicated, and I mean 10 times as complicated as it needs to be, is ridiculous. I consider it irresponsible. This is a safety issue. DJI has put their future competitiveness ahead of safety.
How many times have you heard of an un-explained drone disappearance? The battery manager has the authority to shut the drone down. It is almost statistically impossible that failure of their proprietary flight time system hasn’t been the cause of many of them. It is the most complicated part of the battery manager.
Do you think DJI fesses up about drone incidents caused by battery manager logic failure. The logic should be only: Is the voltage high enough? That’s all. There is not much that will go wrong with that.
YouTube Link:
phantom4 zoom lens telephoto modification Ragecams inspection Search & rescue wa | HD Wearable Video Custom Mods By RageCams
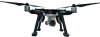
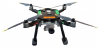
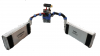
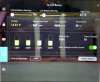
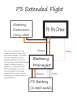
Attachments
Last edited: